Design. Print. Build.
U of I Team Aims to Revolutionize Affordable Housing With 3D-Printed Wood Waste
Article by Alexiss Turner '09, and Alissa Korsak '11,'16
Photos by Melissa Hartley, and Rio Spiering, University Communications and Marketing
Affordable housing is not a luxury, it’s a basic need.
University of Idaho is developing technology to make housing more affordable nationwide by using Idaho wood waste to make one of the most sustainable building construction materials on the market. They’re combining sawdust and other wood byproducts with bio-based glue to create a medium for 3D-printing buildings and stackable bricks.
“We’re trying to change the way houses are built in the United States,” said Michael Maughan, associate professor in mechanical engineering. “It’s too expensive, it takes too long, and we think we can do it with a lot less money, labor and injuries for construction workers.”
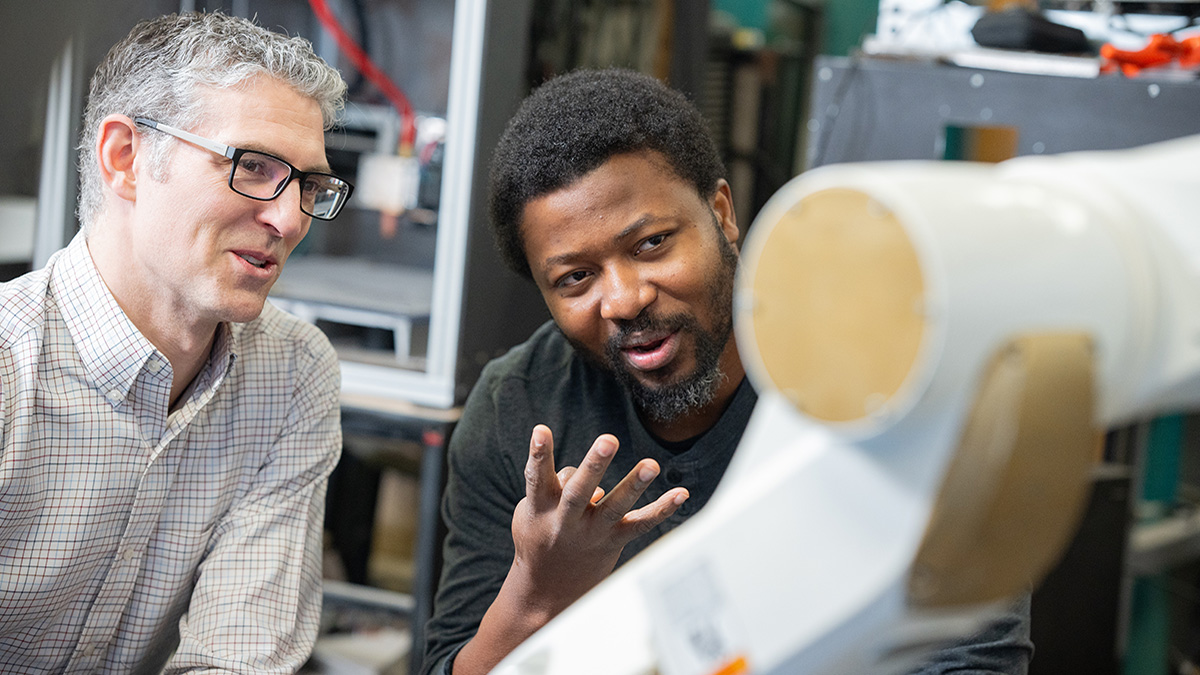
Increased demand, rising building costs, a global pandemic and long-term supply chain disruptions led to some of the largest increases in home prices in recent history, with Idaho and Washington experiencing some of the highest jumps.
The interdisciplinary project, known as PrinTimber, is expected to positively impact Idaho’s fast-growing construction industry. The colleges of Engineering, Natural Resources and Art and Architecture are partnering with Auburn University on the project.
From Sawdust to Shelter
“There’s always an accepted way of doing things,” said Randall Teal, professor and head of the U of I architecture program. “Our faculty and students are trying to look at things differently — to find new ways of doing things, to question them and to use our current discoveries for the greatest good possible.”
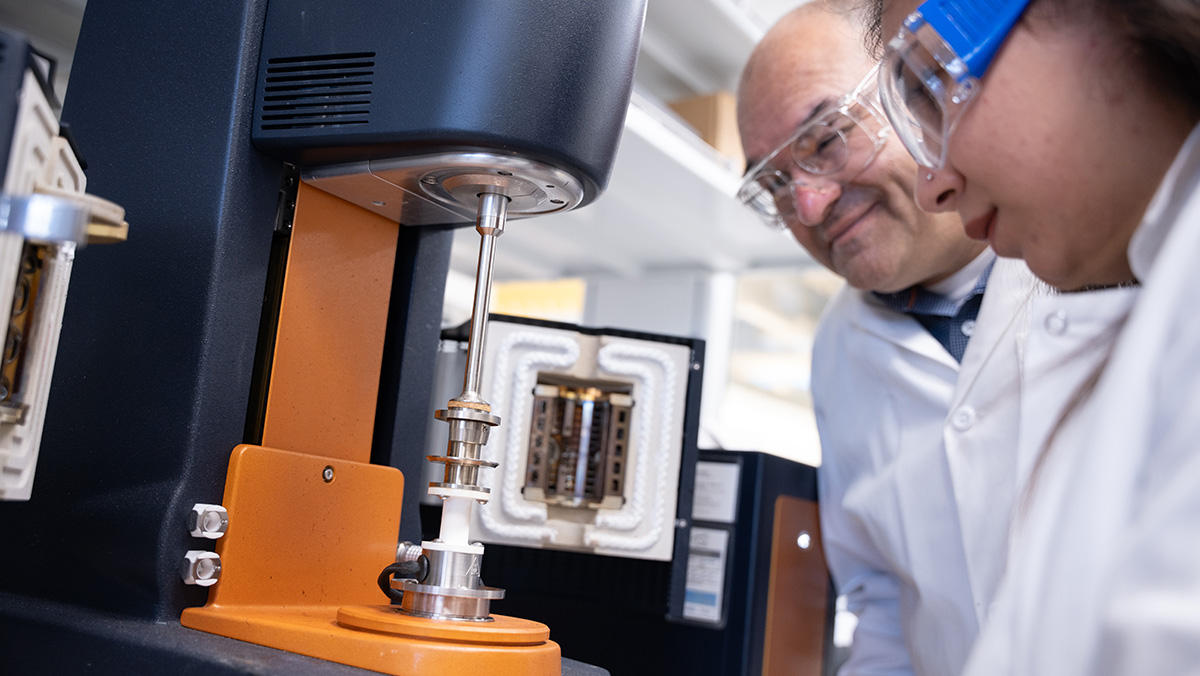
Faculty members from the colleges of Art and Architecture and Natural Resources brainstormed an idea that reduces the nation’s affordable housing problem and fosters sustainable industry practices. They wanted to 3D print a house using natural materials, specifically sawdust and wood waste, which are readily available in Idaho from mills and wood processing plants. Nationally, U.S. lumber manufacturing generates 84 million tons of sawmill dust and waste per year.
“Only about 40% of a tree is converted into lumber,” Maughan said. “That means there’s a lot of waste that’s either left in the forest or used for lower-value products.”
The team brought in U of I engineers and renewable material specialists to develop a construction material based on wasted wood fibers. They also needed to create a 3D printer prototype and the glue — called resin — to hold the wood fibers together.
Everything is a tradeoff. Any change we make to the wood-to-resin ratio and the chemical or organic breakdown of the resin itself affects how the material runs through the printer, how fast the material cures, how strong the material is and how much it can withstand environmental factors. Armando McDonald, professor of renewable materials chemistry
Robert Carne, a mechanical engineering doctoral student, and other students on the team, are developing and testing a 3D printer capable of producing structural walls for a house out of sawdust and resin as a prototype for industrial use. The goal is to create a large-scale, mobile printer capable of printing construction elements for a home with little human interaction on the construction site.
“Before pursuing my graduate degree, I worked in residential construction. It’s dangerous, you work long hours, and it’s extremely expensive to build a home,” Carne said. “That’s the most important thing to me: being part of the old way of doing things and blazing the trail using a renewable resource.”
3D printing with an abrasive material like sawdust is very different from using smooth plastic filament typical in hobby 3D printing. The engineering team is refining a custom printer design and a continuous layering method to adhere the layers of the printed material using a specialized resin.
The team wants to create a plant-based resin to bond the wood fibers together. If they succeed, the new construction material will be completely bio-based, as wood is already a renewable natural resource.
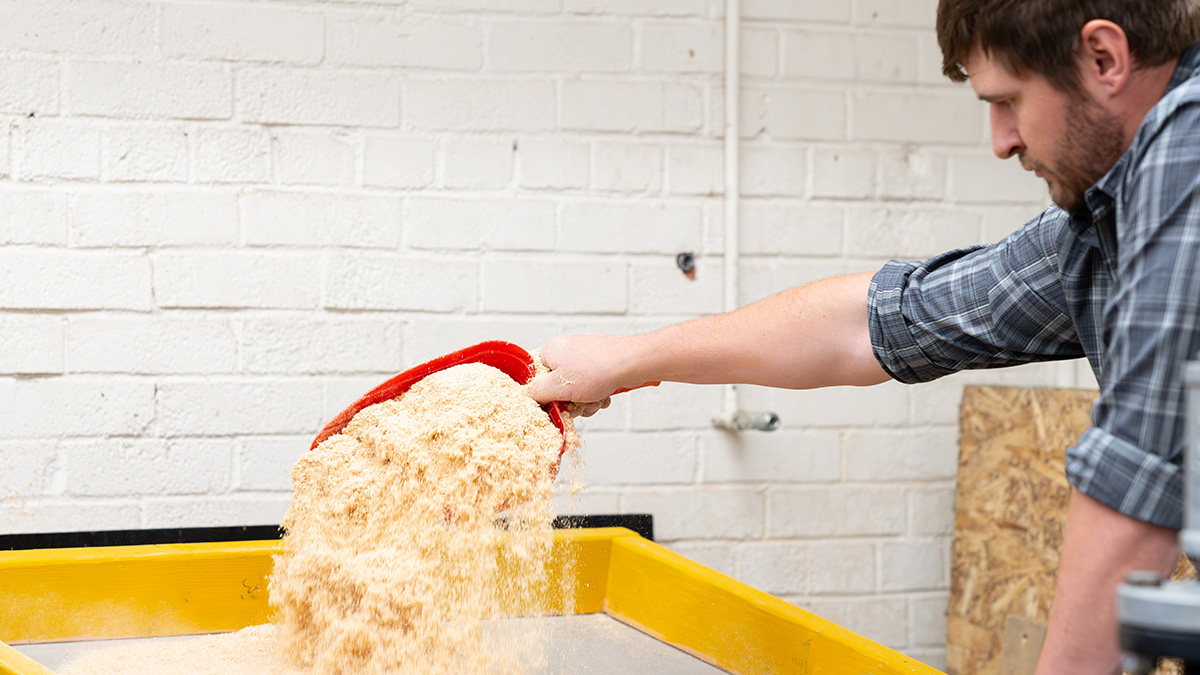
Once the substance cures, it needs to be strong, heat resistant and insulating — the same quality indicators of any building construction material. An added challenge is ensuring the uncured wood and resin mixture can be easily pushed through the 3D printer.
“Everything is a tradeoff,” said Armando McDonald, professor of renewable materials chemistry. “Any change we make to the wood-to-resin ratio and the chemical or organic breakdown of the resin itself affects how the material runs through the printer, how fast the material cures, how strong the material is and how much it can withstand environmental factors.”
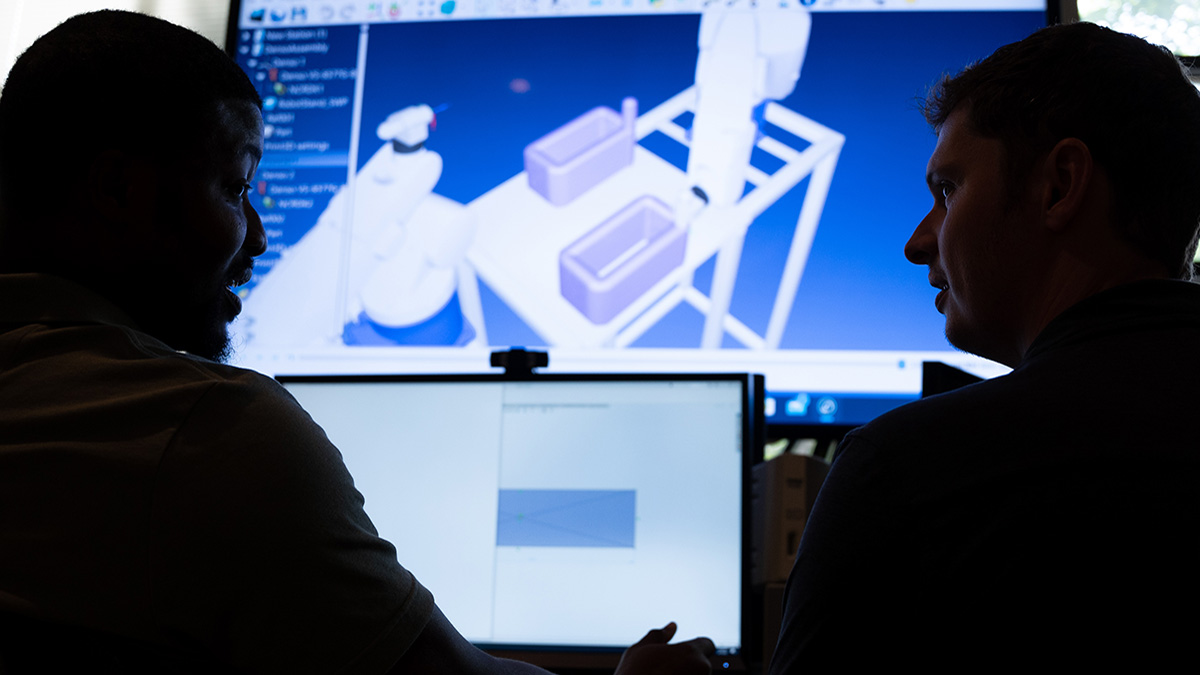
McDonald is working with partners at Auburn University to analyze how different plant-based and synthetic resins react to pressure, heat and other elements to identify the best binding agents.
The team’s bio-based wood and resin will be energy efficient compared to recent 3D printing construction ventures using concrete. Concrete requires a large amount of heat to create a dry powder ready for mixing, which releases carbon dioxide into the atmosphere. The PrinTimber material doesn’t require this energy.
“No one else is using novel composites in the way we are,” McDonald said. “Our research team is incredible, we’re nimble, we interact, we get things done.”
Timber Tech
3D printing the wood and resin mixture takes several hours, so graduate students on the PrinTimber team started thinking of ways to test the material without putting it through the printer.
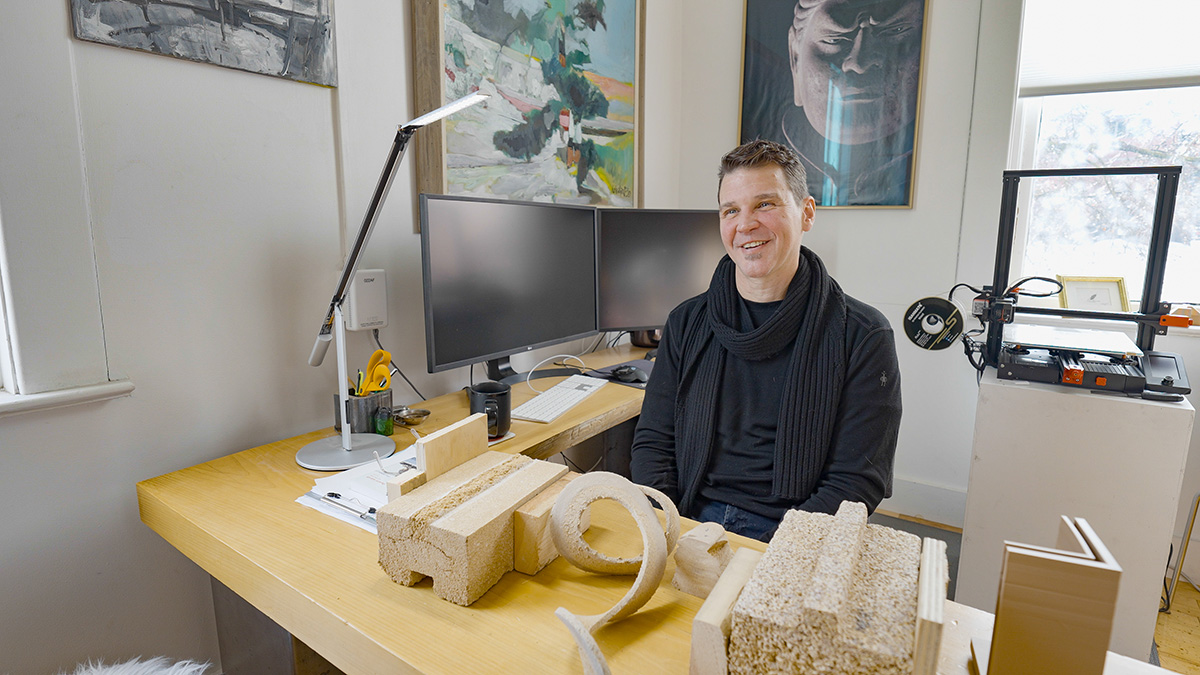
They devised a stackable brick, known as the TechnoLog, formed with the same material used in the 3D printing process. Compressed into a brick shape and allowed to cure, this material is showing promise as a second construction method.
“With the PrinTimber project, we’re really hoping to address the needs at every level and make a meaningful impact,” Teal said. “The TechnoLog will hopefully provide an easy-to-use, low-tech product that allows for an easy entry point for use within the construction industry.”
Architecture master’s students Mallory Bermensolo, Jim Severt and Tavia Dahl took first place in Fall 2023 with the TechnoLog product in Boise State University’s Entrepreneur Week’s Hacking for Homebuilding Pitch Competition. The team earned $9,000 in the statewide contest.
U of I Boise faculty and graduate students are researching the product and exploring how it can fill gaps in the construction industry.
“Our research here in Boise is focused on state-of-the-art review, testing and showcasing PrinTimber to larger audiences through events like Hacking for Homebuilding and international conferences,” said Dahl. “Through engagement with the local and international community, we create a feedback loop. This allows us to design and create something as a team that can fill gaps in the industry.”
Getting real-time feedback from industry experts allows us to pivot and redirect our strategy as needed so we’re not wasting time. Additionally, listening to what others are doing and what the needs of the market are allows us to be creative in the solutions we provide. Mallory Bermensolo, U of I Boise architecture master's student
Bermensolo knows how important this feedback loop is to the project and interviews industry experts, building code specialists and local builders to understand how the product fits market needs.
“Getting real-time feedback from industry experts allows us to pivot and redirect our strategy as needed so we’re not wasting time,” said Bermensolo. “Additionally, listening to what others are doing and what the needs of the market are allows us to be creative in the solutions we provide.”
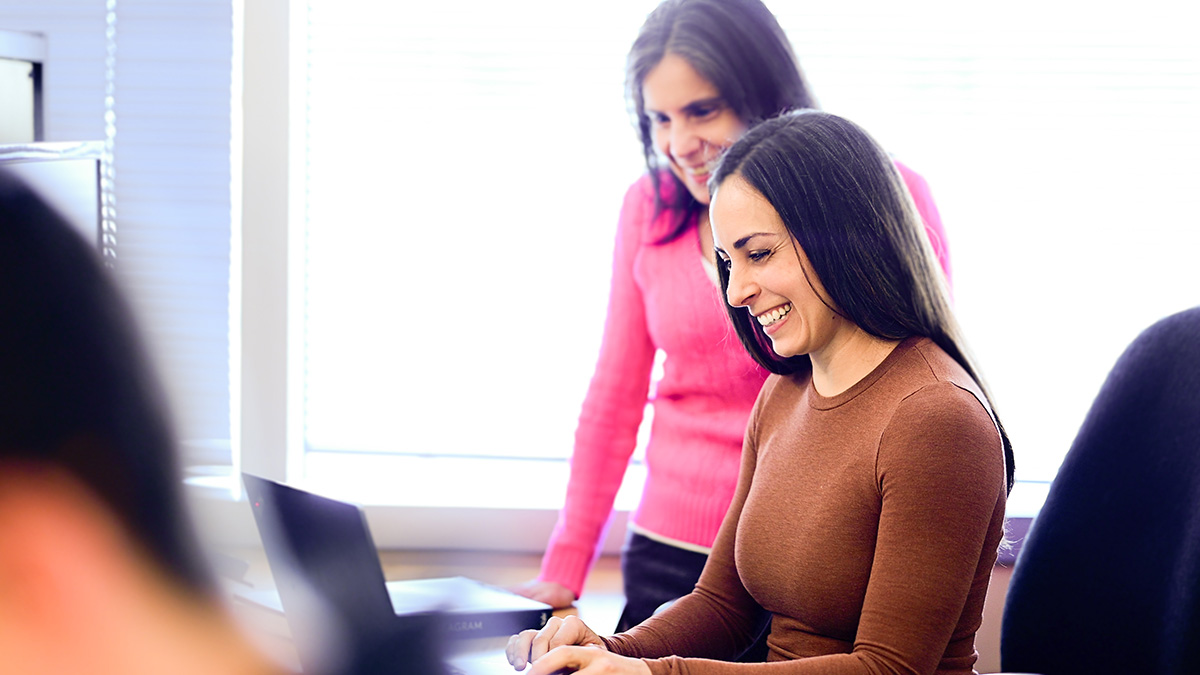
Dahl values the team’s commitment to sustainability, resiliency and the emphasis on waste as a valuable resource.
“The opportunity to be part of such an innovative project has been really exciting,” said Dahl. “Others have worked with wood waste, but PrinTimber is dedicated to creating a product that is 100% biobased, circular and cost effective — and I get to contribute to that.”
This spring, the team plans to construct a small shed using TechnoLogs in the Lupine Flats community in Moscow — a planned community being built on land owned by Moscow Affordable Housing Trust. Future plans include building an entire small house with the product. The TechnoLog would become an additional pathway for sustainable homebuilding, adding to the multimillion-dollar research already conducted under the PrinTimber project.
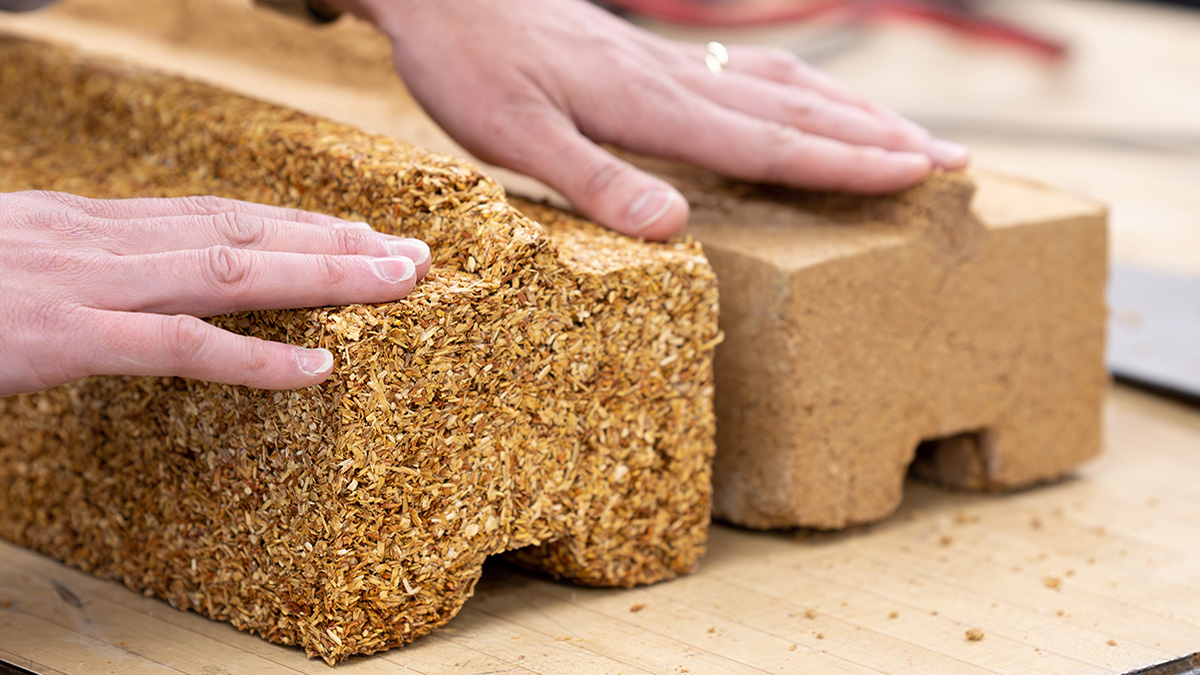
Published in April 2024.